Extreme Pressure (EP) grease is a specialized lubricant formulated to endure the high loads and extreme conditions often encountered in heavy machinery and commercial vehicles. Effective lubrication is vital for maintaining the functionality, efficiency, and longevity of equipment, especially in demanding environments. This guide covers the properties, applications, and best practices for using EP grease, allowing operators and fleet managers to make informed decisions about their maintenance strategies.
What Is EP Grease?
EP grease is designed to provide superior protection against wear and mechanical failure in applications where traditional lubricants might fall short. It typically contains unique additives that enhance its properties, making it suitable for heavy-duty applications.
Key Characteristics of EP Grease:
- Base Oils: The primary component of EP grease, typically derived from mineral or synthetic sources. Synthetic oils are often preferred due to their superior performance in extreme temperatures.
- Thickeners: Commonly lithium-based, these give the grease its consistency and help it adhere to surfaces, reducing the likelihood of dripping or washing away.
- Additives:
- Extreme Pressure Agents: These compounds, such as molybdenum disulfide (commonly referred to as “Moly”,) significantly enhance the grease’s ability to withstand high loads. Research indicates that a concentration of around 5% Moly can provide critical protection by forming a protective film on metal surfaces.
- Anti-Wear Additives: To minimize friction and prevent metal-to-metal contact, these substances help maintain equipment integrity.
- Corrosion Inhibitors: These protect metal surfaces from rust and degradation in harsh operating environments.
For a detailed look at the performance characteristics of EP lubricants, refer to this study published on ScienceDirect.
EP grease is commonly used in a variety of applications, including bearings, gears, and other mechanical systems that experience significant loads and harsh conditions.
Applications of EP Grease
EP grease is well-suited for various industries, including construction, mining, agricultural, and automotive sectors. Here are some typical scenarios where EP grease is indispensable:
1. Heavy Machinery
In construction and mining, equipment such as excavators and bulldozers operate under heavy loads and harsh environments. EP grease is used in critical joints, bearings, and hydraulic systems to ensure smooth operation and prevent failures.
2. Automotive Use
For vehicles, particularly those involved in towing or heavy hauling, EP grease is utilized in components such as wheel bearings and U-joints to provide a protective barrier against wear under high stress.
3. Agricultural Equipment
Agricultural machinery, which often works in dusty or moist conditions, relies on EP grease for its ability to resist washout and maintain performance even under varying climates.
4. Industrial Equipment
In manufacturing settings, EP grease is widely used on conveyor belts and other machinery where operational reliability is paramount.
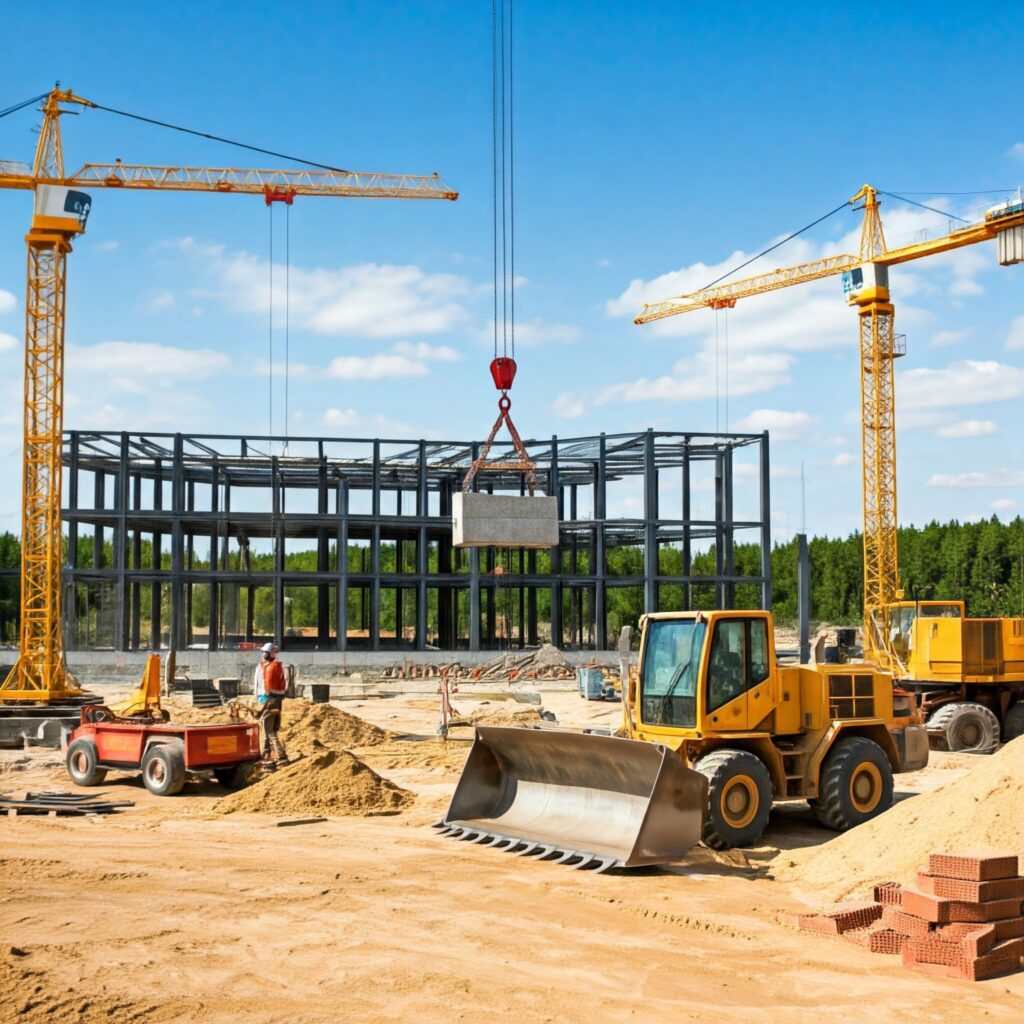
Comparing Leading EP Grease Brands
Selecting the appropriate EP grease can have significant ramifications for performance and reliability. Below is a comparative analysis of three reputable EP grease brands:
1. AMSOIL NLGI #2 Synthetic Polymeric Off-Road Grease
AMSOIL’s EP grease is formulated with high-purity synthetic base oils and advanced additive technology, including 5% molybdenum disulfide. This product offers excellent thermal stability and resistance to water washout, making it ideal for heavy-duty applications.
- Key Feature: Contains approximately 5% Moly, providing outstanding protection against wear.
- Best Application: Off-road vehicles and heavy machinery facing extreme conditions.
2. Mobilgrease XHP 222
Mobilgrease XHP is recognized for its performance in both automotive and industrial applications. It is engineered with EP properties to address the needs of high-load situations while protecting against corrosion and oxidation.
- Key Feature: Excellent water resistance and adhesion.
- Best Application: Industrial applications and vehicles in challenging environments.
3. Shell Gadus S3 V220
Shell Gadus provides reliable performance in a variety of applications, emphasizing versatility and performance in both high and low temperatures. This grease is suitable for multiple applications, ensuring consistent performance.
- Key Feature: Robust protection from wear and water washout.
- Best Application: General-purpose grease for a wide range of applications.
Grease Brand | Key Strengths | Recommended Use |
AMSOIL NLGI #2 | Superior protection, extended life | Off-road and heavy-duty machinery |
Mobilgrease XHP 222 | Water resistance and corrosion protection | Heavy equipment and automotive use |
Shell Gadus S3 V220 | Versatile performance across temperatures | Multi-purpose lubrication |
Practical Tips for Using EP Grease
- Understand Application Requirements: Always check the equipment’s manual to determine the appropriate lubrication needs, including EP grease specifications.
- Proper Application: Apply EP grease using the correct tools such as grease guns. Over-greasing can lead to pressure build-up and leakage.
- Regular Inspection: Periodically check greased components for wear or damage to ensure they are functioning properly.
- Compatibility Checks: Make sure the EP grease is compatible with existing lubricants in your equipment to avoid chemical reactions that can impair performance.
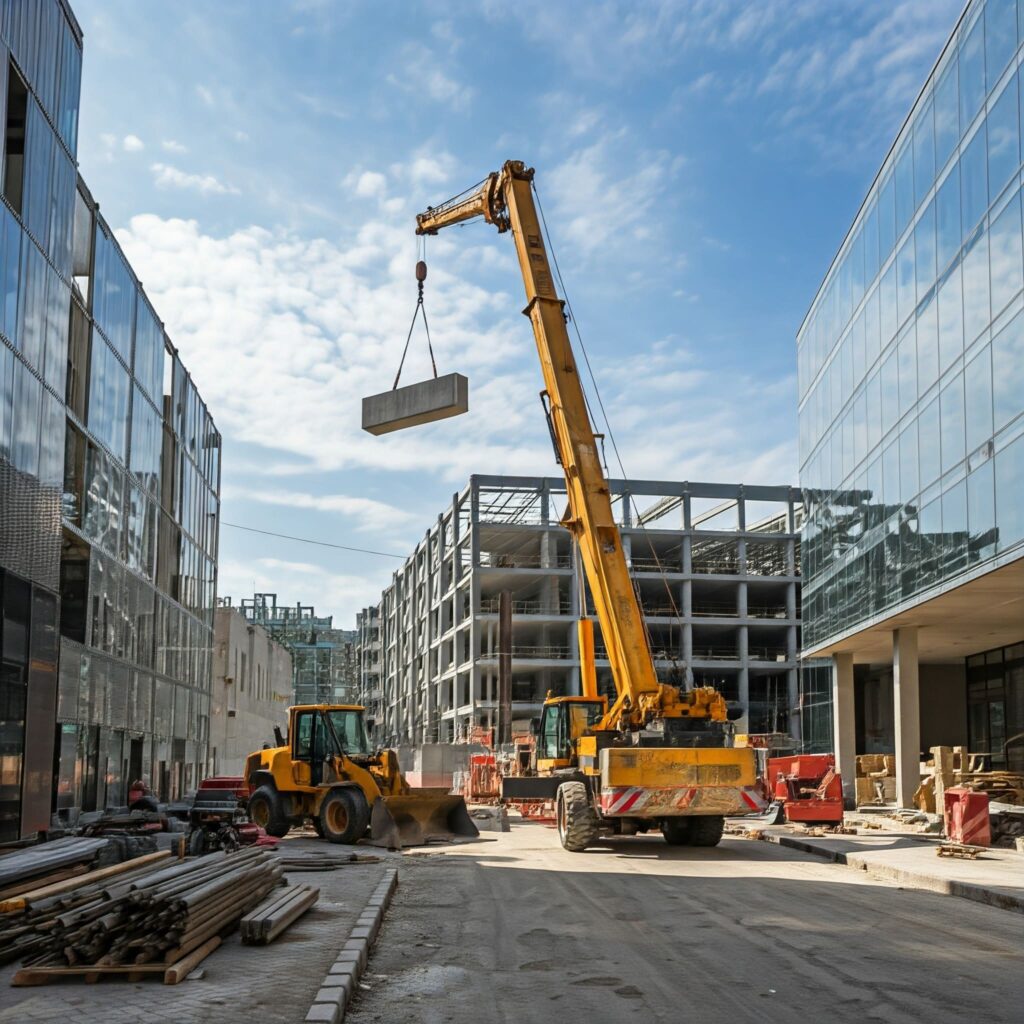
Frequently Asked Questions
1. What are the benefits of using EP grease?
EP grease provides enhanced protection against wear, oxidation, and rust, especially in high-pressure applications.
2. Can I use EP grease in all applications?
No, EP grease is designed for specific applications involving extreme pressure. Always refer to equipment manuals for lubrication recommendations.
3. How often should I apply EP grease?
Frequency of application depends on the specific equipment and usage levels. Regularly monitor lubrication levels and condition.
4. Is AMSOIL EP grease suitable for my vehicle?
AMSOIL EP grease is compatible with a wide range of vehicles and equipment. Consult your vehicle manual to confirm compatibility.
Conclusion: Ensuring Engine and Component Longevity
Selecting the right EP grease is critical for protecting machinery and ensuring optimal performance, especially in demanding applications. Brands like AMSOIL, Mobil, and Shell provide dependable solutions that meet the rigorous requirements of modern vehicles and equipment.
By understanding the properties and appropriate uses of EP grease, you can make informed decisions that ultimately lead to improved reliability and reduced maintenance costs. Investing in quality lubrication is pivotal for extending the lifespan of your equipment and maintaining peak performance under pressure.