Engine oil pumps are vital components in maintaining engine performance and longevity. They ensure proper lubrication by circulating oil under the correct pressure to protect moving parts from friction and wear. This guide explores the types of oil pumps, their mechanisms, challenges they present, and the characteristics of oil best suited for optimal engine operation.
Types of Engine Oil Pumps
Different engines utilize different oil pump designs to suit specific operational needs. Here’s a breakdown of the most common types:
1. Gear-Type Oil Pump
- How It Works: Common in older engines like the Chevy 350, these pumps use rotating gears to generate constant oil flow and pressure.
- Strengths: Reliable and durable.
- Challenges: The gear action can stress oil through shear forces, requiring oils with high shear stability.
2. Rotor-Type Oil Pump (Gerotor)
- How It Works: Combines an inner rotor and outer rotor to create a compact and efficient pumping mechanism. As the rotors rotate, oil is pressurized before being pushed through the oil galleries.
- Strengths: Compact size, reliable performance, and widely used in modern engines.
3. Crescent-Type Oil Pump
- How It Works: Features an outer gear rotating around a stationary crescent-shaped spacer. Oil flows into gaps between the gear teeth, gets compressed, and exits under pressure.
- Strengths: Simple and effective design that generates high pressure consistently.
Each pump type performs a critical role in maintaining oil circulation and engine health. Understanding these differences can help you assess the specific needs of your engine.
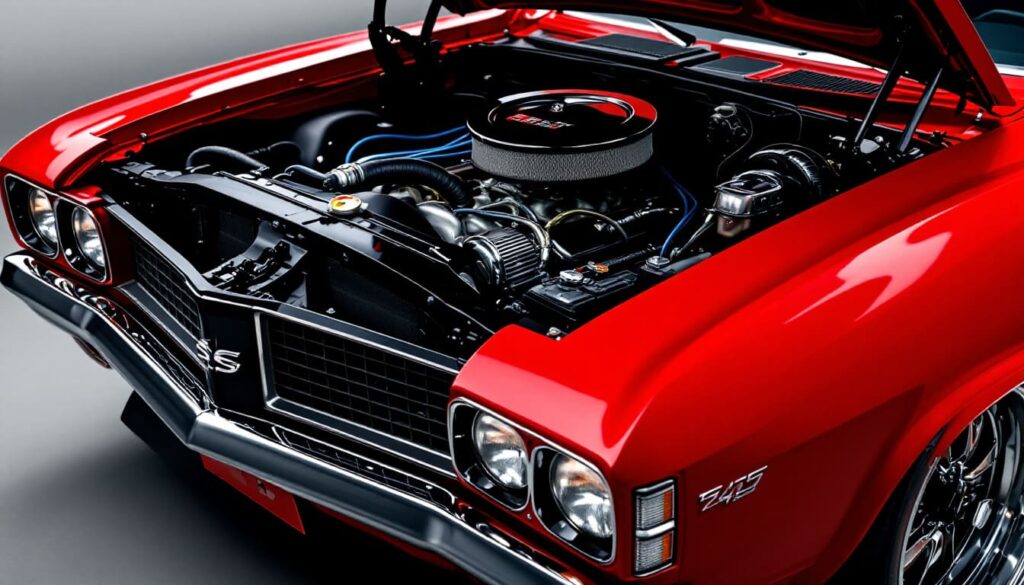
The Function and Importance of Oil Pumps
Oil pumps are typically located near the bottom of the engine to draw oil from the sump. Their key functions include:
Maintaining Oil Pressure: By pressurizing the oil, the pump ensures it can reach all engine components, including bearings and moving parts.
Lubricating Engine Components: Proper lubrication minimizes friction, enhances engine efficiency, and reduces wear and tear.
Cooling the Engine: Oil helps carry heat away from critical components, complementing the engine’s cooling system.
Challenges Oil Pumps Present
Despite their importance, oil pumps also introduce unique challenges that impact engine oil performance:
Shearing and Pressure Points
The pump’s internal mechanisms create shear forces that can break down oil molecules. This results in lowered viscosity, reducing the oil’s ability to form a protective film.
Heat Generation
Friction and pressure within the pump generate heat, further impacting the oil. The oil used must resist thermal breakdown to maintain its properties under stress.
Effects of Oil Pumps on Engine Oil
The mechanical and thermal stress introduced by oil pumps significantly affects engine oil.
- Shear Stress: Repetitive chopping or pressing of oil molecules reduces its viscosity over time. For example, a 30-weight oil may degrade to a 20-weight, compromising lubrication.
- Molecular Stability: Poor-quality oils are more vulnerable to breaking down under pump stresses, whereas synthetic oils maintain their structure for longer periods.
To combat these effects, high-quality synthetic oils, such as those from AMSOIL, Mobil 1, and Castrol EDGE, are specifically formulated to resist shearing and thermal degradation.
Key Characteristics of Quality Engine Oil
For an oil pump to operate efficiently, the engine oil must meet specific standards:
- Shear Resistance: Oils should retain their viscosity under high-pressure conditions. Synthetic oils excel in this area, minimizing viscosity loss over time.
- Thermal Stability: High heat resistance ensures the oil remains effective even under extreme temperature fluctuations generated by the pump.
- Balanced Additives: Additives such as anti-wear agents and dispersants enhance the oil’s ability to protect engine components and withstand stress.
These characteristics ensure long-term engine reliability and optimal pump performance.
Consequences of Oil Pump Failures
Pressure Points and Shearing
Oil pumps, by their nature, create pressure points that can shear oil molecules. This shearing action reduces the viscosity of the oil, potentially degrading from a 30 weight to a 20 weight, which compromises its protective properties.
Heat Generation
Pumping oil generates significant heat, which can further affect the oil’s viscosity and overall performance. The oil used must be capable of withstanding these temperature changes to maintain engine protection and efficiency.
Effects of Oil Pumps on Oil
The design and operation of oil pumps create a chopping action that affects oil molecules. Over time, this can reduce the oil’s viscosity, impacting its ability to lubricate and protect engine components. A high-quality oil designed to be shear-resistant can mitigate these effects, maintaining its protective qualities for longer periods.
Importance of Strong Oil
To ensure an oil pump functions correctly without compromising the engine, the oil must be robust. This means the base oil itself must be extremely durable and present in the right amounts. A well-rounded product, like AMSOIL, is designed to handle the shearing forces within the pump while maintaining good oil pressure and lubrication properties.
Oil Composition for Pump Performance
The strength of the oil starts with its composition. High-quality base oils and additives must be blended in precise ratios to offer optimal performance. This ensures the oil can withstand the mechanical stresses and heat generated by the oil pump, providing consistent protection and performance.
Heat Generation in Oil Pumps
Heat is an inevitable byproduct of oil pump operation. The friction and pressure generated while pumping oil cause a rise in temperature, which can alter the oil’s viscosity. Quality oils are formulated to remain stable under these conditions, ensuring they continue to lubricate effectively.
Oil Requirements for Pump Function
For an oil pump to function properly and provide adequate lubrication:
- Heat Resistance: The oil must withstand the heat generated by the pump.
- Pressure Maintenance: The oil must maintain proper viscosity under pressure.
- Lubrication Properties: The oil must lubricate all engine components without breaking down.
Consequences of Oil Pump Failure
If an oil pump malfunctions, the results can be catastrophic:
- Zero Oil Pressure: A failed pump means oil cannot circulate, leading to immediate issues such as overheating and lack of lubrication.
- Rapid Component Wear: Without proper lubrication, engine components can seize, resulting in significant damage.
- Costly Repairs: Replacing or repairing damage caused by oil pump failure often involves extensive labor and high costs.
By using high-quality oils and adhering to regular maintenance schedules, you can prevent many pump-related issues and ensure your engine continues to run smoothly.
FAQs About Engine Oil Pumps
What type of oil is best for high-performance oil pumps?
Synthetic oils are ideal due to their superior shear resistance and thermal stability under high-stress conditions.
How often should I check my oil pump’s performance?
While there’s no exact schedule, checking oil pressure during routine maintenance can help detect pump issues early.
Can oil pumps affect fuel efficiency?
Yes. An efficient oil pump ensures proper lubrication, reducing friction and improving overall engine efficiency.
Key Takeaways
- Oil Pumps Are Essential: They maintain oil pressure, provide effective lubrication, and enhance engine cooling.
- Pump Types Matter: Gear, rotor, and crescent pumps each have strengths suited to specific engine designs.
- Quality Oil Is Crucial: Oils with strong shear resistance and thermal stability protect both the pump and engine.
- Regular Maintenance Prevents Failures: Routine checks and proper oil choice ensure engine longevity and minimize downtime.
By understanding how oil pumps function and the demands they place on engine oil, you can make informed decisions to protect your vehicle’s performance and reliability.