Molybdenum disulfide, or moly, is a mineral-based compound with unique properties that have made it an ideal lubricant for heavy equipment. Whether you operate bulldozers, excavators, or other demanding machinery, moly grease offers exceptional protection against extreme pressure, high heat, and heavy shock loads.
This comprehensive guide explains everything you need to know about moly grease, from its science to specific applications and product recommendations.
What Is Molybdenum Disulfide?
Molybdenum disulfide (MoS2) is a naturally occurring mineral often used in greases and lubricants for its superior friction-reduction capabilities. Sourced from molybdenite ore, more than 60% of the world’s moly supply comes from the Rocky Mountains in Colorado.
Key Properties of MoS2:
- High Heat Resistance: With a melting point of 4,370°F, moly can endure temperatures far beyond standard lubricants.
- Load-Bearing Capacity: Laboratory tests reveal moly can withstand up to 500,000 pounds per square inch (psi) of pressure.
- Layered Molecular Structure: The lamellar (layered) design enables moly to act like a deck of sliding cards, reducing friction and wear under heavy loads.
Why Is Moly Grease a Game-Changer for Heavy Equipment?
The layered molecular structure of moly provides a unique advantage for lubrication. Here’s why moly grease is worth considering:
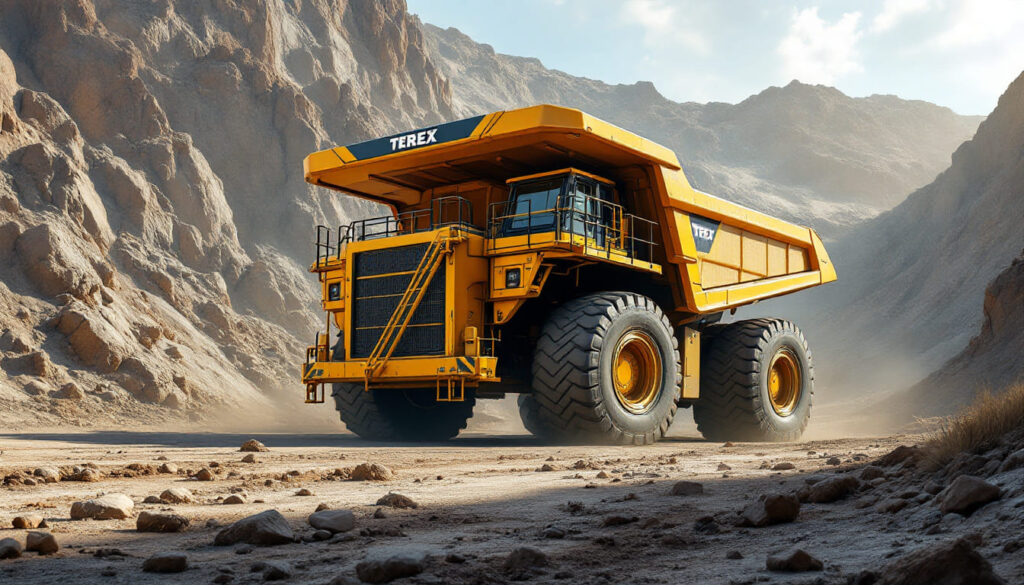
1. Exceptional Friction and Wear Reduction
Moly plates itself onto metal surfaces during high-pressure and high-heat applications, filling microscopic gaps to create a smooth, protective layer. This prevents wear even in environments where traditional lubricants would break down.
2. Resilience to Extreme Pressure and Shock Loads
Unlike regular grease, moly grease absorbs shock loads that can exceed 500,000 psi. This property makes it ideal for heavy machinery operating under constant stress, such as truck axles, backhoes, and hydraulic systems.
3. Performance in High Temperatures
Moly grease functions optimally at temperatures as high as 700°F. This allows it to withstand the intense heat generated by heavy-duty equipment.
Real-World Testing: The Proven Benefits of Moly Grease
Study 1: Fleet Vehicle Wear Reduction
The Southwest Research Institute tested moly grease across 38 police cars, buses, and semi-trucks over two years. Results included:
- A 26-38% reduction in wear for police car chassis points.
- A significant 18-88% wear reduction for components such as kingpins, u-joints, and shackles on larger vehicles.
Study 2: Commercial Bakery Fleet
A commercial bakery used moly grease in wheel bearings across its 200+ vehicle fleet. After three years:
- Wheel bearing failures were virtually eliminated, reducing maintenance costs significantly.
These controlled studies confirm that moly grease reduces repair downtime while extending the life of critical components.
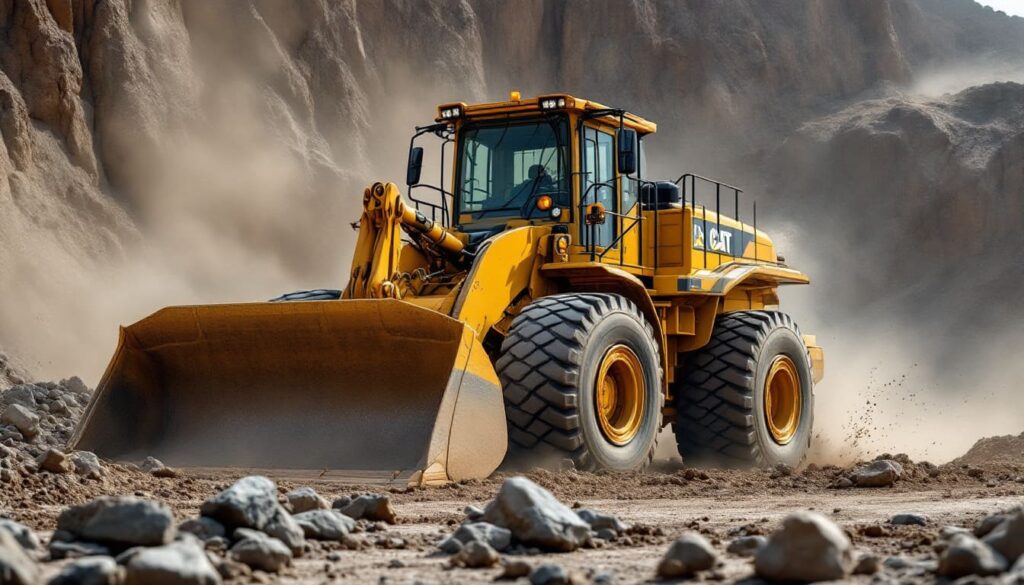
Applications of Moly Grease
Moly grease has practical applications across industries, including construction, mining, fleet management, and even aerospace. Common uses include:
- Ball Joints and Kingpins: Protects these critical points from wear under constant heavy load.
- Hydraulic Systems and Bearings: Reduces heat and friction in high-use components.
- Dusty or Harsh Environments: Ideal for equipment used in environments where standard greases harden or degrade, thanks to moly’s resilience to oxidation.
In fact, moly grease has even been tested and trusted by NASA for its ability to operate at both cryogenic and high-vacuum conditions.
Top Moly Grease Products for Heavy Equipment
1. AMSOIL Synthetic Polymeric Off-Road Grease
- Features: Contains 5% moly for extreme pressure resistance, high-temperature performance, and excellent water washout shielding.
- Best For: Off-road machinery in mining, agriculture, and construction.
- Notable Advantage: Extended lubrication intervals.
2. CAT Extreme Pressure Grease
- Features: Includes 3-5% moly and complies with Caterpillar’s stringent grease requirements.
- Best For: Caterpillar machinery or other OEM equipment operating under high load stresses.
- Notable Advantage: Superior bonding for fleet-level durability.
3. Mobilgrease XHP 322 Moly
- Features: A lithium-complex grease with 2% moly, designed for moderate-duty applications.
- Best For: Smaller equipment fleets or medium-duty vehicles needing cost-effective lubrication.
- Notable Advantage: Balances cost with performance.
FAQs on Moly Grease
1. Does higher moly content mean better performance?
Not always. For most general applications, a moly content of 1-5% is sufficient. Higher concentrations are reserved for extremely specialized uses, such as aerospace or ultra-heavy loads.
2. Can moly grease reduce maintenance costs?
Yes. Moly grease extends re-greasing intervals and reduces wear on components, significantly lowering repair and replacement costs over time.
3. Should I only use synthetic moly grease?
Synthetic greases are best for extreme temperatures and high-stress environments but may not be necessary for all applications. Evaluate your equipment’s specific operational demands.
Conclusion: Why Moly Grease Should Be a Maintenance Essential
Moly grease is a practical solution to some of the most common challenges faced by heavy equipment operators. Its ability to reduce friction, withstand extreme pressures, and perform in high temperatures makes it a significant upgrade over traditional greases.
While AMSOIL’s Synthetic Polymeric Off-Road Grease outshines competitors for extreme-duty applications, options like CAT Extreme Pressure Grease and Mobilgrease XHP 322 are strong picks for specific needs.
Investing in quality moly grease means fewer breakdowns, longer equipment life, and reduced downtime—benefits that translate directly into cost savings and peace of mind.