Maintaining heavy-duty farm machinery and off-road vehicles with the right grease is vital for their optimal performance and longevity. A comprehensive understanding of their lubrication needs is crucial, as different machines may require specific types of grease to function efficiently. Neglecting this aspect or using improper grease can lead to subpar performance, an increased risk of equipment breakdowns, and result in costly repairs and prolonged downtime.
Selecting the appropriate grease ensures that moving parts operate smoothly, significantly minimizing wear and tear. For instance, using a high-temperature grease for components exposed to heat prevents the grease from breaking down under extreme conditions. Conversely, a water-resistant grease is critical for equipment frequently exposed to moisture and rain, as it prevents rust and corrosion.
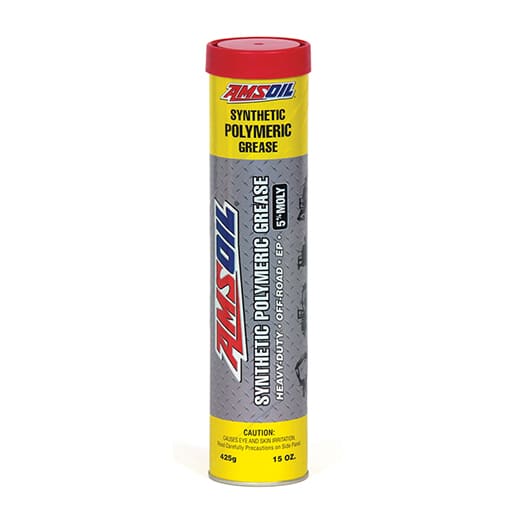
Furthermore, consistent and correct lubrication is imperative in protecting equipment from extreme temperatures and harsh environmental conditions. Cold weather can cause grease to thicken, making it less effective, while high temperatures can thin the grease, reducing its protective capabilities. Therefore, it’s essential to choose a grease with the appropriate viscosity and additives suited to both the operating environment and the specific machinery.
It’s easy to underestimate the importance of this seemingly small detail, yet neglecting proper lubrication can have a ripple effect on your farm’s overall productivity and your financial situation. By preventing unnecessary wear, reducing the likelihood of breakdowns, and extending the lifespan of your equipment, the right grease fundamentally supports the smooth running of farm operations, safeguarding both your investments and your income.
Lubrication Schedules
OEM recommendations for greasing schedules often fail to account for several critical factors such as heavy or harsh usage, your company’s specific maintenance practices, and diverse environmental conditions. For example, machinery operating in dusty or wet environments may require more frequent lubrication than what the OEM guidelines suggest. Dust particles can infiltrate the lubricant, impairing its ability to reduce friction, while moisture can lead to rust and corrosion, further compromising the equipment’s performance.
Moreover, your organization’s unique maintenance routines play a pivotal role in determining the effectiveness of these schedules. Whether your maintenance protocols are thorough and consistent or occasional and sporadic, these habits can significantly affect equipment longevity. A company with a robust maintenance system might still need to adjust the OEM schedule for optimal performance, while a firm with less consistent practices might find that strict adherence to OEM guidelines is insufficient.
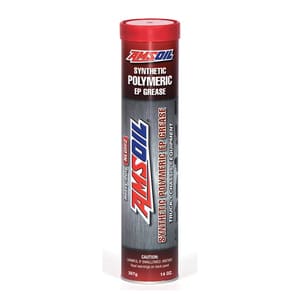
Failing to customize lubrication schedules to meet these specific operational and environmental needs can result in premature equipment failure, costly repairs, and unnecessary downtime, which in turn affect production efficiency and profitability. Therefore, it’s imperative to develop tailored lubrication schedules that align precisely with your actual working conditions and maintenance capabilities, ensuring that all variables are considered to maximize equipment lifespan and operational efficiency.
Just as car manufacturers recommend specific schedules for oil changes, the prescribed grease intervals for off-road equipment often don’t consider the benefits of using high-quality lubricants. Standard guidelines usually cater to the average product, not factoring in advancements in lubricant technology. Premium greases can safely extend the time between greasings, reducing both maintenance demands and downtime. Traditional schedules, typically conservative, aim to prevent worst-case scenarios rather than optimize performance. By opting for superior grease, equipment operators can achieve longer-lasting protection, meaning they won’t need to maintain machinery as frequently. This not only boosts operational efficiency but also slashes costs and enhances equipment longevity. Furthermore, investing in high-quality lubricants significantly cuts down on wear and tear, leading to fewer breakdowns and repairs. These benefits far outweigh the initial cost, making it a smart choice for anyone looking to maximize their machinery’s potential.
Adhering to OEM guidelines lays an excellent foundation for establishing effective maintenance routines. However, it’s crucial to recognize that unique environmental conditions and specific equipment situations can significantly impact lubrication frequency. For instance, machinery operating in harsh climates with extreme temperatures, such as icy winters or sweltering summers, may require more frequent lubrication than what the manufacturer recommends. Similarly, equipment exposed to high levels of dust or sand, as found in mining or construction sites, might necessitate additional attention to ensure optimal performance. Additionally, machinery handling heavy loads or running continuously in industrial settings could experience increased wear and tear, thus needing more regular lubrication than standard intervals suggest. It’s imperative to assess these variables meticulously to ensure machinery operates at peak efficiency and to prevent unexpected downtime. Neglecting to adjust maintenance routines in response to these factors could lead to premature equipment failure and costly repairs, underscoring the importance of tailoring lubrication practices to the specific demands of the operating environment.
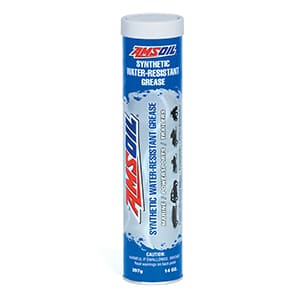
Maintenance issues with grease fittings often arise due to their placement in hard-to-reach areas, making regular servicing difficult. Operators frequently overlook these essential maintenance tasks or forget altogether, leading to insufficient lubrication. Many times, the equipment isn’t greased as often as it should be, resulting in accelerated wear and tear. Additionally, using the incorrect type of grease can compromise the efficiency and longevity of machinery, causing further complications.
Most heavy-duty farm machinery is equipped with numerous grease fittings, commonly known as zerks, that require regular lubrication to ensure both optimal performance and longevity. These zerk fittings, however, are notoriously difficult to locate and are often placed in hard-to-reach spots, posing a significant challenge even for the most experienced maintenance staff. Such inconvenient placement can result in delays and inefficiencies during routine servicing, which can potentially compromise the machinery’s overall functionality and lifespan. The challenge is further compounded by the variability in zerk placement across different models and brands of machinery, making a one-size-fits-all approach to maintenance impractical.
Therefore, it’s crucial for maintenance teams to not only be well-trained in identifying these fittings but also to stay up-to-date with industry-specific best practices. Adequate training should include hands-on sessions that cover the various locations of zerk fittings on different types of machinery. Additionally, maintenance personnel need to be equipped with specialized tools designed to access these hard-to-reach areas efficiently, such as flexible grease guns and extension hoses. By addressing these considerations, maintenance teams can perform lubrication tasks more effectively, minimizing downtime and ensuring the machinery operates smoothly and reliably over the long term.
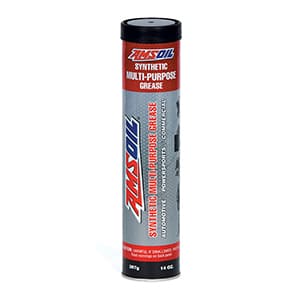
Neglecting to pay attention to numerous hidden fittings often leads to overlooked grease points, which can rapidly increase component wear. Over time, this negligence accelerates the deterioration of these parts, ultimately causing them to fail and forcing equipment to sit idle. Such oversights disrupt operations, leading to costly downtime and extensive repairs. This situation can be particularly problematic in industries where machinery uptime is critical, such as manufacturing and transportation. Maintaining vigilance in identifying and servicing these fittings is crucial for preventing premature wear. Regular inspection and lubrication of all fittings, including those that are less visible, ensure the longevity of your equipment. Furthermore, a proactive maintenance approach can minimize unplanned interruptions and extend the life cycle of your machinery, thereby optimizing operational efficiency.
Reapplying grease is necessary after a specific number of operational hours for most fittings. This frequency can vary based on factors such as heavy usage and environmental conditions like dust, humidity, and temperature fluctuations. Each piece of equipment may have its own unique maintenance schedule, and sometimes even different fittings on the same machine require their own specific lubricating intervals. These differences can be due to varying loads, speeds, or exposure to harsh conditions. For instance, a fitting that operates under a heavy load might need more frequent lubrication compared to one that experiences lighter use.
As the number of grease applications increases, keeping track of all these maintenance schedules can become quite challenging. A meticulous record-keeping system is essential to ensure every fitting gets the attention it needs at the right time. This organized approach helps prevent equipment failures and extends the lifespan of the machinery. Additionally, neglecting proper lubrication schedules can lead to increased wear and tear, which may result in costly repairs and downtime. Therefore, implementing a structured maintenance plan and diligently recording each lubrication task is crucial for optimal equipment performance and reliability.
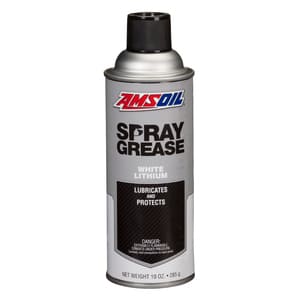
Choosing the right grease is essential for maintaining your equipment’s performance and longevity. Greases formulated with different thickening systems can cause significant damage if used together. When incompatible greases are mixed, they may either solidify or become excessively runny, thereby compromising the protective layer your machinery relies on. This inconsistency in texture leads to higher rates of wear and tear, diminished operational efficiency, and ultimately, expensive repairs. For instance, a grease that becomes too hard may no longer circulate properly, leaving parts unprotected. Conversely, a grease that becomes too soft may leak out, failing to provide the necessary lubrication. In either case, the equipment’s efficiency and lifespan are at risk. Therefore, checking for compatibility is not just a precaution; it’s a critical step in ensuring the smooth and efficient operation of your machinery. By doing so, you can effectively prevent degradation and avoid unexpected maintenance costs, ultimately safeguarding your investment.
Operational challenges encompass various issues such as grease being forced out under the pressure of heavy loads, which reduces its effectiveness. Additionally, the ingress of dirt and other contaminants can severely compromise machinery by creating abrasive conditions and accelerating wear. Moreover, water washout can lead to lubrication failures by washing away the grease, leaving components unprotected and prone to rust and corrosion. These factors collectively undermine the reliability and efficiency of machinery, necessitating frequent maintenance and potentially costly downtime.
The constant pounding action during daily operations puts significant stress on equipment pivot points, causing lower-quality greases to be displaced. When this displacement occurs, the lubrication that is supposed to separate metal parts is no longer present, resulting in increased wear and tear on the components. Over time, this leads to the gradual degradation of these metal surfaces.
Additionally, when the lubricant seal is compromised, it not only fails to keep the moving parts protected but also allows water and abrasive contaminants to infiltrate. This moisture and debris can cause rust, corrosion, and pitting on the metal surfaces, exacerbating the wear process. The presence of these harmful elements accelerates the deterioration of the equipment, often culminating in total component failure. So, it’s crucial to use high-quality greases that can withstand the stresses and maintain their integrity to ensure the longevity and reliability of the machinery.
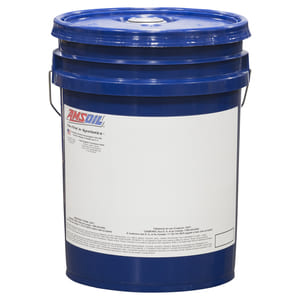
Heavy-duty agricultural and off-road equipment frequently encounters harsh environmental conditions such as water, dirt, dust, mud, and sand. These contaminants can easily infiltrate the system when grease lubrication isn’t sufficient, leading to accelerated wear and tear on critical components. For instance, dirt can erode the surfaces of moving parts, while water can induce rust, both of which significantly degrade the efficiency of the machinery. Over time, this constant exposure to foreign materials can break down seals, clog filters, and compromise the overall integrity of the equipment. This deterioration not only diminishes performance but also leads to costly repairs and extended downtime. To mitigate these risks, implementing proper lubrication protocols and adhering to a rigorous maintenance schedule are essential. Regular checks and timely interventions help ensure the equipment’s longevity and reliability, ultimately safeguarding operational productivity and reducing unexpected expenses.
When low-quality grease comes into contact with water, it can easily wash away from crucial equipment parts, exposing them to unnecessary risks. This lack of adequate lubrication results in increased metal-on-metal friction, leading to accelerated wear and tear of components. Over time, this wear can significantly reduce the lifespan of machinery, potentially causing parts to fail prematurely.
Furthermore, exposed metal surfaces become more vulnerable to rust and corrosion due to moisture. This corrosion doesn’t just weaken the structural integrity of the machinery; it also leads to further deterioration and inefficiency. The combined effects of wear and corrosion create a vicious cycle that raises maintenance costs and increases the likelihood of unexpected equipment failures. Such failures can result in costly downtime, disrupt operations, and necessitate the replacement of expensive parts. Therefore, the importance of using high-quality grease that can withstand water exposure cannot be overstated in maintaining the longevity and reliability of industrial equipment.
AMSOIL Synthetic Polymeric Off-Road Grease provides top-tier protection, effectively addressing issues resulting from neglected grease points and missed lubrication schedules. Unlike standard greases, it remains in place significantly longer, ensuring consistent lubrication over extended periods. This leads to reduced maintenance needs, less downtime, and increased equipment lifespan, all while maintaining optimal performance even in the harshest conditions. Its superior formulation resists washout and adheres firmly to surfaces, making it especially advantageous in demanding off-road environments where reliability is critical. The grease’s ability to withstand extreme pressure and high-impact situations further enhances its suitability for heavy-duty applications, ensuring that machinery operates smoothly under stress. By resisting water and contaminants, it also helps prevent rust and corrosion, which are common issues in off-road settings. This comprehensive protection reduces the likelihood of unexpected failures, ensuring that equipment remains operational and efficient.
AMSOIL Synthetic Polymeric Off-Road Grease delivers enhanced lubrication and significantly extends maintenance intervals for grease points on off-road equipment. Ideal for high-stress applications, this grease excels in lubricating heavily loaded pivot points, bushings, articulation points, machine implements, universal joints, driveline grease points, and wheel bearings across a wide range of machinery. Using a calcium-sulfonate complex thickener, it ensures peak performance while maintaining compatibility with other thickeners, such as those based on lithium-complex formulations.
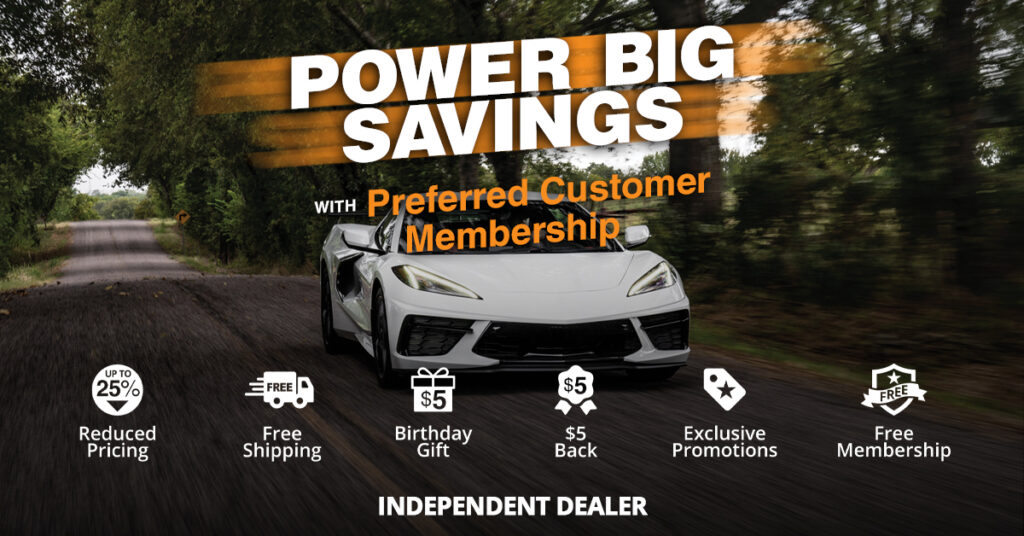
Its advanced composition offers superior resistance to water washout, ensuring reliability even in wet and muddy conditions. The grease also withstands extreme pressure, reducing wear and tear on critical components. Furthermore, its resistance to oxidation prevents the formation of deposits, which can impair machinery efficiency over time. This combination of features makes AMSOIL Synthetic Polymeric Off-Road Grease a dependable choice for those looking to maximize the lifespan and functionality of key off-road machinery parts, thereby reducing downtime and maintenance costs.
AMSOIL Synthetic Polymeric Off-Road Grease is specially designed to withstand severe pound-out conditions, ensuring that machinery maintains optimal lubrication even during the most strenuous high-pressure and heavy-impact operations. Its strong adhesion and cohesion properties allow the grease to remain firmly in place, even under wet conditions and during rigorous cleaning processes, providing unmatched continuous protection. It performs exceptionally well in water washout tests, attaining an impressive score of 1% (ASTM D1264), demonstrating its superior ability to prevent water from contaminating metal parts. This advanced grease not only protects components by reducing wear but also significantly extends the lifespan of equipment used in demanding off-road and high-stress environments. It addresses the unique challenges posed by such conditions, making it an indispensable choice for maintaining the longevity and efficiency of heavy-duty machinery.
AMSOIL Synthetic Polymeric Off-Road Grease provides exceptional sealing properties that effectively prevent abrasive particles from infiltrating pivot joints, ensuring enhanced protection and extending the lifespan of equipment. With 5% molybdenum disulfide in its composition, this grease creates a robust barrier, maintaining a distinct separation between metal parts. Even when lubrication intervals are missed, it continues to offer strong protection, a critical safeguard for the longevity and reliability of off-road machinery. This is especially important under challenging conditions where consistent maintenance might be difficult, such as in muddy or dusty environments that can accelerate wear and tear.

The formulation is specifically designed to endure the rigorous demands of off-road environments, promoting operational efficiency and reducing the likelihood of mechanical failures. For instance, construction vehicles frequently subjected to heavy loads and uneven terrain benefit significantly from the added durability and protection this grease provides. Similarly, agricultural equipment operating in harsh, dirty conditions is less likely to suffer from joint wear or component seizure. By effectively sealing pivot joints, this grease minimizes the risk of contaminants entering vital areas, thereby contributing to reduced maintenance costs and downtime.
In addition, incorporating 5% molybdenum disulfide not only reduces friction but also enhances the load-carrying capacity of the grease, making it ideal for high-stress applications. This feature is particularly beneficial for machinery that operates under extreme pressures or temperatures, where traditional greases might fail. The advanced formulation ensures that even in the toughest off-road conditions, equipment remains protected and operational, thus maximizing productivity and minimizing the risk of unexpected breakdowns.
Conclusion: Maximizing Farm Equipment Lifespan
If you’re wondering, “What Is the Best Grease for Farm Equipment?”, choosing the right product is essential for maximizing lifespan and efficiency. AMSOIL bearing and chassis greases are designed to tackle the toughest conditions, ensuring smooth operation. By investing in high-quality grease, you safeguard your machinery, reduce maintenance costs, and ensure optimal performance. Check out AMSOIL’s full line for reliable solutions.
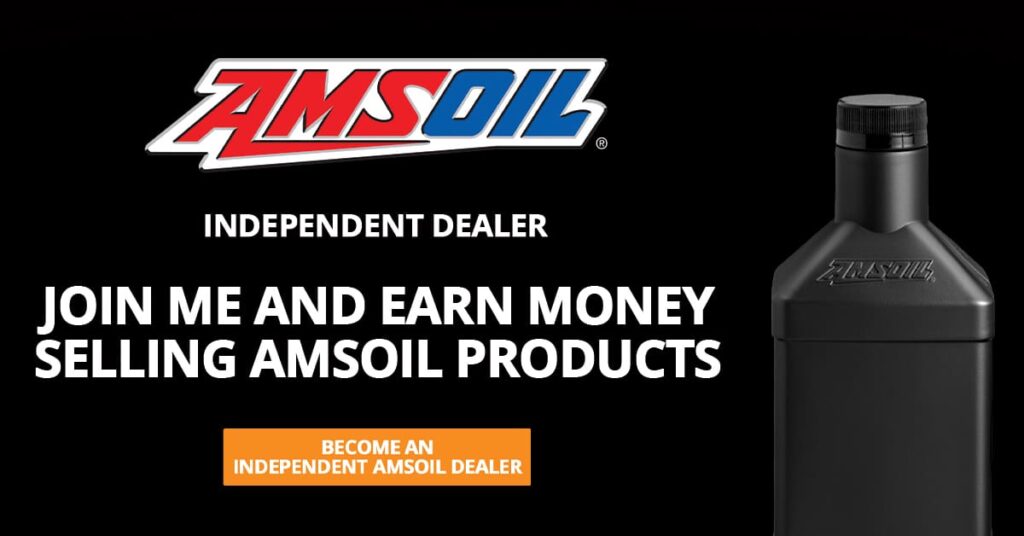