When you’re picking out the best synthetic greases for your needs, it’s crucial to consider various factors such as viscosity, thickener composition, and the specific working conditions. These elements play a vital role in determining the most appropriate grease for different applications. Grease consists of three key components: base oil, thickeners, and additives. The National Lubricating Grease Institute (NLGI) utilizes a classification system that is penetration-based. NLGI #2, the most commonly used grade, is extensively utilized in automotive and heavy-duty environments, like ball joints and suspension components. NLGI #2 grease is a popular choice among many users. The NLGI scale spans from #000, which is akin to the texture of cooking oil, to #6, as dense as cheddar cheese. Understanding these distinctions is crucial for choosing the right grease for specific machinery and equipment.
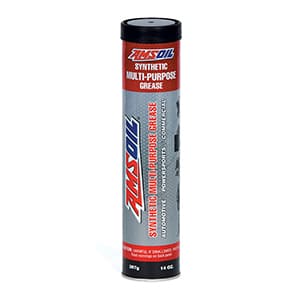
NLGI# | Penetration | Consistency | Food Analogy |
000 | 445 – 475 | Fluid | Cooking Oil |
00 | 400 – 430 | Semi-Fluid | Applesauce |
0 | 355 – 385 | Very Soft | Brown Mustard |
1 | 310 – 340 | Soft | Tomato Paste |
2 | 265 – 295 | “Normal” Grease | Peanut Butter |
3 | 220 – 250 | Firm | Vegetable Shortening |
4 | 175 – 205 | Very Firm | Frozen Yogurt |
5 | 130 – 160 | Hard | Smooth Paté |
6 | 85 – 115 | Very Hard | Cheddar Cheese |
It is crucial to carefully consider the performance specifications when selecting grease for automotive applications. The grease industry has established specific standards for different types of greases, such as chassis greases (designated as LA and LB) and wheel bearing greases (indicated by GA, GB, and GC).
For instance, if you come across a grease labeled as GC-LB, it signifies that it has successfully met the most rigorous testing requirements for both chassis components and wheel bearings. Greases meeting this GC-LB specification are typically designed to not only comply with the stringent industry standards but also satisfy the demands of various car manufacturers. This ensures optimal performance and longevity for automotive parts subjected to diverse operating conditions.
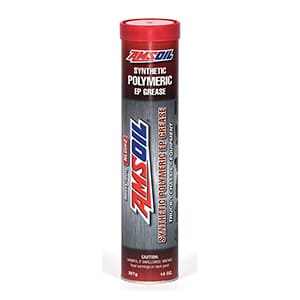
When considering the most suitable grease for a particular application, it is crucial to take various factors into account. The type of thickener, consistency, dropping point, temperature range, worked stability, oxidation stability, and wear resistance all play significant roles in determining the effectiveness of the lubricant. However, the viscosity of the grease remains the most critical aspect, usually selected based on the specific requirements of the application at hand.
One common mistake in the selection of grease is confusing grease consistency with the viscosity of the base oil. It is essential to carefully evaluate the application conditions, environmental factors, operating speeds, applied loads, and adhere to the recommendations provided by the original equipment manufacturer (OEM) to ensure optimal performance.
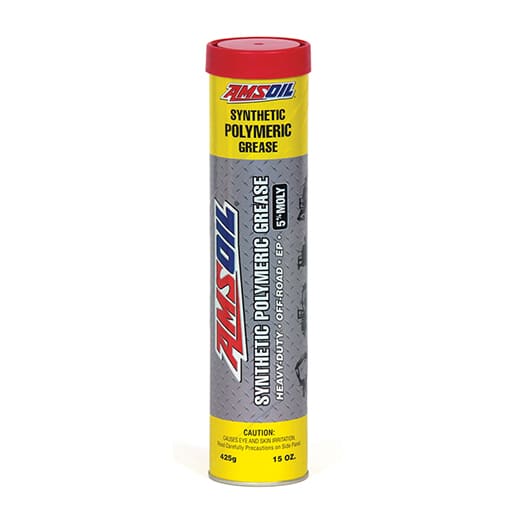
To elaborate further, different applications may call for specific types of grease to be used. For example, high-speed machinery may require grease with excellent stability under high temperatures, while heavy-duty equipment might benefit from grease with superior wear resistance. By considering these factors and selecting the appropriate type of grease, the efficiency and longevity of the machinery can be significantly enhanced.
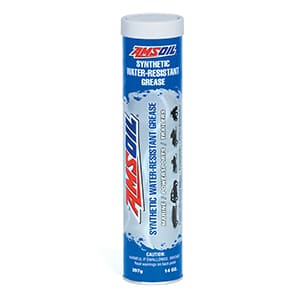
The realm of rotating bearings encompasses a wide range of vital components crucial for various applications. These components include roller bearings, plain bearings, thrust bearings, gears, electric motors, presses, winches, bushings, wheel bearings, chassis lubrication, universal joints, ball joints, tie-rod ends, and steering knuckles. Found in manufacturing facilities, automobiles, trailers, landscaping equipment, agricultural machinery, and powersports gear, these elements play a significant role in optimizing operational efficiency. To achieve peak performance, selecting the right lubricants is essential. AMSOIL 100% Synthetic Multi-Purpose Grease NLGI #2, AMSOIL 100% Synthetic Water-Resistant Grease, and the high-performance AMSOIL DOMINATOR® 100% Synthetic Racing Grease stand out as exemplary choices for ensuring smooth operations and longevity of rotating bearings.
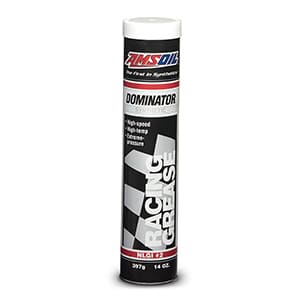
Bearings that are subjected to intense impacts, such as heavily loaded chassis grease points, wheel bearings, axle assemblies, universal joints, pivot pins, steering linkages, spring pins, king pins, ball joints, water-pump bearings, and other greased heavy-duty components, require specialized greases specifically designed for use in heavy-duty machinery that operates in severe conditions. These specialty greases provide superior protection compared to what a general-purpose grease can offer. For applications involving such components, it is recommended to use high-quality greases like AMSOIL NLGI #2 100% Synthetic Polymeric Truck, Chassis, and Equipment Grease, as well as AMSOIL 100% Synthetic High-Viscosity Lithium-Complex Grease. These greases have proven to be highly effective in ensuring optimal performance and longevity of the equipment by safeguarding against wear, corrosion, and extreme pressures, making them ideal choices for demanding industrial environments where equipment reliability is paramount.
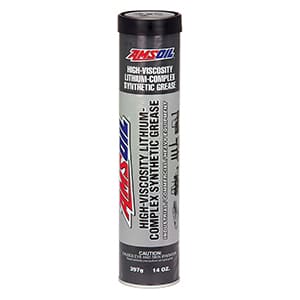
When it comes to non-rotating bearings and sliding scenarios, a robust selection of components such as pivot pins, king pins, bucket pins, fifth-wheel hitch plates, and bushings are essential for heavy-duty applications. Greases specifically engineered for these demanding environments surpass standard multipurpose greases by providing superior protection, impact resistance, and adhesion. These specialized greases are formulated to meet the extreme requirements of these critical components.
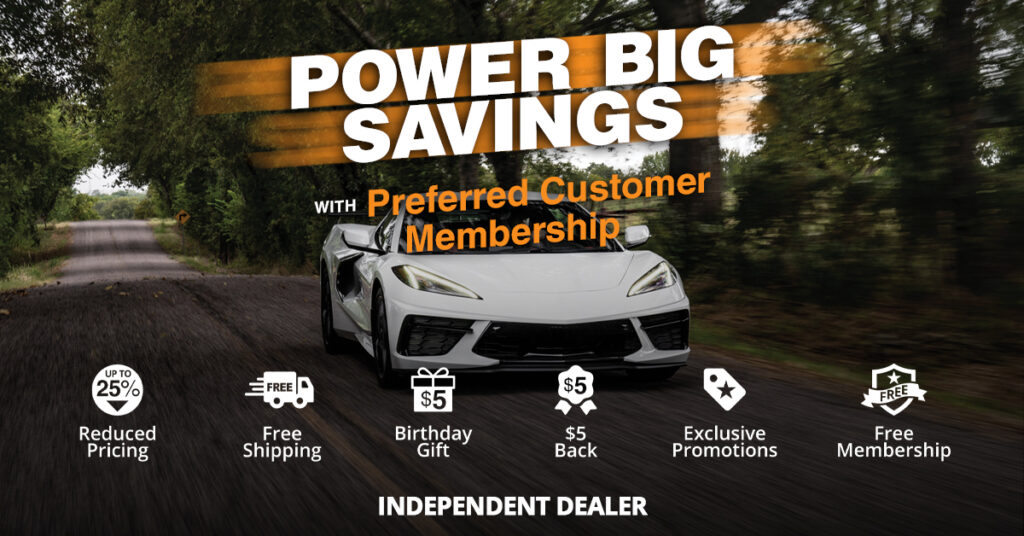
For those seeking top-tier lubrication solutions, AMSOIL offers two exceptional products: the AMSOIL NLGI #2 100% Synthetic Polymeric Off-Road Grease and the AMSOIL NLGI #2 100% Synthetic Polymeric Truck, Chassis, and Equipment Grease. These high-performance greases are designed to excel in challenging conditions, ensuring optimal lubrication and protection for critical mechanical elements subjected to heavy loads and harsh operating environments.
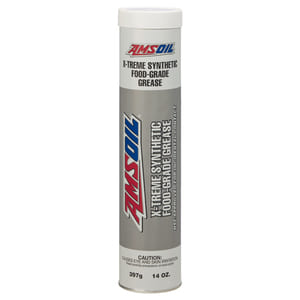
Specialized applications often require machinery tailored for specific industries such as food service or pharmaceuticals. These sectors typically demand the use of NSF-Approved grease, like the AMSOIL X-Treme 100% Synthetic Food-Grade Grease, which is meticulously crafted to withstand a wide range of operating temperatures effectively.

In certain scenarios, specialized equipment, including Arctic drilling rigs, necessitates a grease that offers exceptional pumpability in cold weather conditions. Many conventional greases are ill-equipped to handle below-freezing environments, struggling to maintain proper lubrication and protection at sub-zero temperatures. However, the AMSOIL DOMINATOR® 100% Synthetic Racing Grease sets itself apart with remarkable cold-weather attributes, ensuring optimal torque performance even under extreme low temperatures as low as -40°F.
To sum it up, I trust this blog post provided you with the insights needed to pinpoint the ideal grease for your specific application. Whether you’re grappling with high-temperature environments or heavy-duty machinery, knowing the right synthetic greases to use can make all the difference. By understanding the characteristics of different grease types and matching them to your equipment’s requirements, you can ensure smoother operations and longer-lasting performance. So, next time you’re lubricating those gears and bearings, remember that choosing the right grease is not just a shot in the dark – it’s a calculated move that sets the stage for optimal functionality.
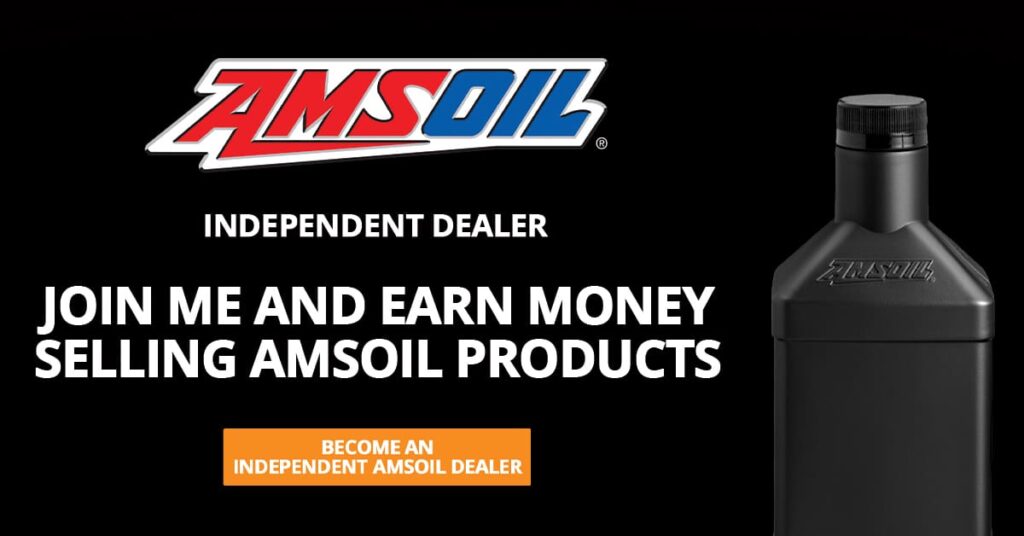